CASE STUDY: CUSTOM FLEECE FOR WIDOW JANE DISTILLERY
Our client, Widow Jane based out of Brooklyn, NY came to us wanting to create a custom wearable sweatshirt that reflected their passion for creating bold, rich whiskey while complementing the unique culture of inner city New York. In a town full of hipsters, artists, intellects, cold weather, and connoisseurs of fine crafted whiskey, Team Phun succeeded in “crafting” the perfect compliment wearable to their unique identity of customers and brand. Read our story below about how we went from concept to completion in under 6 months.
STEP 1: PLANNING
IT ALL STARTED WITH A PLAN. WE WORKED CLOSELY WITH OUR FABRIC SUPPLY CHAIN TO FIND 14 OUNCE PREMIUM FRENCH TERRY FLEECE, WHICH IS NOT TYPICAL IN THE FABRIC MART. WIDOW JANE LIKED AN AMERICAN APPAREL SAMPLE WE SENT THEM WITH SIMILAR FABRIC, SO WE REVERSED THE SUPPLY CHAIN AND FOUND SOMETHING VERY SIMILAR. USING THAT SWEAT SHIRT AS A REFERENCE, WE REVERSE ENGINEERED THE CUT PATTERNS (AND ADDING A FEW MODIFICATIONS OURSELVES) THAT INCLUDED A CUSTOM ZIPPER KANGAROO POCKET.
AFTER THE CUT PATTERNS WERE CREATED, SAMPLE FABRIC SOURCED, WE RAN A DOMESTIC PRODUCTION SAMPLE IN OUR USA SEWING FACILITIES TO HAVE OUR CLIENT REVIEW. UPON APPROVAL, WE SENT THAT FINISHED PIECE TO OUR OPERATION PARTNERS OVERSEAS TO RECREATE THE SAMPLE, YET FOR ANOTHER APPROVAL. FINALLY, AFTER ALL FABRIC WAS CONFIRMED, SAMPLE APPROVED, WE WERE OFF TO THE RACE IN A FULL CUT-SEW PROJECT.
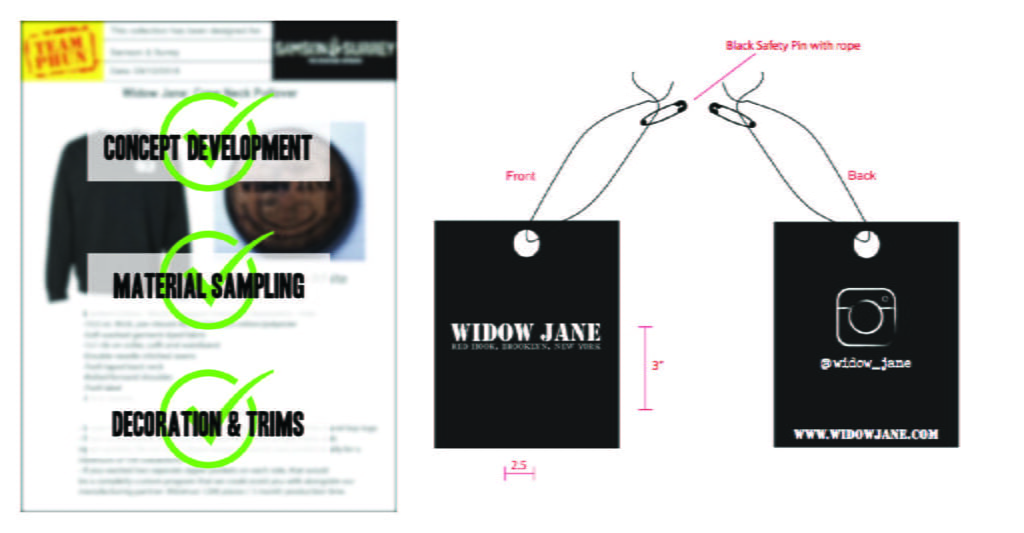
STEP 2: PRODUCTION
FOR A PROJECT SUCH AS THIS, THE FINAL MATERIAL SAMPLING, PRODUCTION, AND SHIPPING TOOK ABOUT 14 -18 WEEKS TO GET THE EXACT PRODUCT THAT WAS APPROVED DURING THE PLANNING STAGE. FOR UNIQUE JOBS LIKE THESE, PRODUCTION TIME DEPENDS ON HOW MANY CUSTOMIZED ELEMENTS ARE INVOLVED WITH YOUR PROJECT. IN THIS CASE, THESE ARE ALL OF THE ELEMENTS INVOLVED:
• We had a unique crewneck sew pattern, sizes Small through 3XL • Completely custom zipper kangaroo pockets that we measured and graded accordingly to fit all sizes appropriately
• Decorations included: Left Chest Embroidery, Back Screen Print, Custom woven neck label with sizes and washing directions, and a custom Retail Hang Tag
STEP 3: QUALITY CONTROL
QUALITY CONTROL PROCEDURES WERE IMPLEMENTED IN BOTH THE SAMPLING PROCESS AND FINAL PRODUCT EVALUATION.
Upon receiving the first round of production samples, we took one of each size and compared it to the American Apparel crewnecks that this project was modeled after, to make sure each size of crewneck matched up with the American Apparel crewnecks. We also checked to see if the custom pockets were the correct size for each size of crewneck. If there were any discrepancies, we let the factory know at this time so that the errors can be addressed before full production of the garments.
Once we received all of the final completed crewnecks, we opened 10% of the packages to assure that all details were correct. Confirming that all was good to go, we counted all the sizes to make sure the inventory was accurate. We then packaged and shipped them to their final distillery destination!
STEP 4: FINAL PRODUCT
WE WERE SO PLEASED WITH THIS LIMITED EDITION PROJECT! THE MOST EXCITING PART FOR US IS THE FINAL PHOTOSHOOT WHERE WE GET TO DOCUMENT THE PHRUITS OF OUR LABOR. THIS CREWNECK IS INCREDIBLY COMFORTABLE, AND THE ZIPPER KANGAROO POCKETS MAKE IT SO CONVENIENT TO THROW YOUR KEYS / WALLET / AND WHATEVER ELSE IN THERE SECURELY SO YOU CAN GO ABOUT YOUR DAY WITH YOUR HANDS FREE TO HOLD YOUR GLASS OF WHISKEY.